کاربردهای انواع شمش فولادی
شمش فولادی یکی از کاربردیترین انواع شمش در جهان است. مطالعه تاریخ نشان میدهد ساخت شمش برای اولینبار در زمان هخامنشیان انجام شده است؛ اما ساخت شمش تنها مربوط به هخامنشیان نبوده است و اکتشافات باستانی نشان میدهد استفاده شمش طلا و نقره به عنوان پول در جهان رواج داشته است.همه ما احتمالا در فیلمها و یا تصاویر ضبط شده از بانکهای بزرگ جهانی هرمهای چیده شده از شمش طلا را دیدهایم.
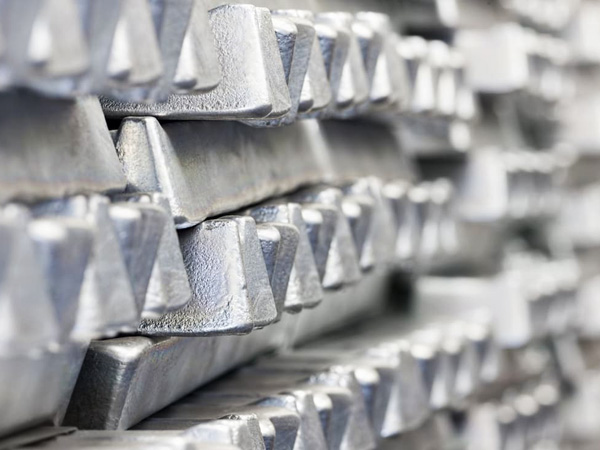
شمشهای زرد طلا که به شکل منشور چهارپهلو که مانند آجر رویهم قرار گرفتهاند، چنین ایماژی تصویریترین تعریف از شمش است که میتوان بیان کرد؛ اما یکی از صحیحترین تعریفها توسط فرهنگ مریام وبستر بیان میشود: «حجمی از فلز که در فرآیند ریختهگری به شکل یک قالب مشخص تولید میشود تا حمل و نقل، ذخیره کردن و استفاده از فلز آسانتر اتفاق بیفتد.»
زنجیره صنعت فولاد وابستگی مستقیم به شمش فولادی دارد. کاربرد شمش فولادی در تولید میلگرد، تیرآهن، ورق فلزی و موارد دیگر استفاده میشود، اما خود شمش مستقیم به چنین تولیداتی تبدیل نمیشود؛ بلکه فرآوردههای میانی تولید فولاد است که به میلگرد، تیرآهن و…. تبدیل میشود.
تولید بیلت بلوم اسلب در ایران و جهان
اگرچه اقتصاد جهان متلاطم و دچار رکود شده است؛ اما المانها نشانگر رشد درخواست جهانی فرآوردههای میانی تولید فولاد است، طبق گزارش روزنامه دنیای اقتصاد نرخ درخواست اسلب در جهان در حال افزایش است، ضمن آنکه بیلت نیز مانند اسلب با رشد درخواست مواجه بوده است.
فراموش نباید کرد که این فرآوردهها در تولید میلگرد، تیرآهن و ورقهای فلزی نقش اساسی دارند و با رشد اقتصاد و فعالشدن بازارهای جهانی بعد از موج کرونا، تولید در بخش ساختمان و صنایع اتومبیلسازی بالاتر خواهد رفت، برای همین نیاز به فلزات ذکر شده بالاتر خواهد رفت.
در کشور ایران نیز سال گذشته نرخ تولید بیلت و بلوم، رشد داشته است؛ بهطوری که اکثر کارخانههای تولیدی نرخ رشد بیلت بالاتر از سالهای قبل بوده و تولید اسلب در ایران از مرز ۷ میلیون تن گذشته است.
اگرچه برای ایران آینده بازار کمی سخت است، زیرا هنوز مسائلی مانند برجام و انتخابات ریاستجمهوری در سال آینده مشخص نیست و پیشبینی بازار برای سال آینده سخت است؛ اما شواهد نشان میدهد رکود تورمی در ساختمان در سال آینده بر درخواست میلگرد و تأثیرگذار باشد و درخواست برای بیلت و بلوم را کاهش دهد؛ بنابراین انتظار میرود همچنان تولید اسلب در آینده نیز بالا باشد.
آنالیز شمش فولادی برای تولید میلگرد
برای تولید میلگرد سایز پایین و سایز بالا مهمتر از سایز شمش، میزان کربن موجود در شمش و آنالیز آن است. البته این مورد تنها برای استاندارد میلگرد آجدار است. استانداردهای خاص خود را دارند. برای میلگرد سایز 14 تا 40 از شمش با کربن 30 تا 35 استفاده می شود. برای سایزهای پایین تر به خاطر نیاز به نرمی و کشش بیشتر از شمش کم کربن استفاده می شود.
شمش 150 و 125 و یا 130 برای تولید میلگرد با یکدیگر تفاوتی ندارند و بعضی کارخانه ها با توجه به خط نورد از شمش 150 استفاده و شارژ می کنند و بعضی دیگر از کارخانه ها هم با شمش 125 بعضی ها هم مدرن تر هستند از هر دو استفاده می کنند. به این معنا که از شمش بلوم نیز برای تولید میلگرد استفاده می شود و بستگی به طراحی خط نورد دارد. خط جدید با تکنولوژی بالا در تولیدی های بزرگ تر و مدرن تر که از هر دو شمش استفاده می کنند ممکن است برای میگردهای ریز از شمش 120 و یا 130 و برای میگرد درشت از شمش 150 استفاده نمایند.
تفاوت شمش 3sp و 5sp
شمش های فولادی در دو گرید معروف 3sp و 5sp تولید شده که این دو محصول در آنالیز و کاربرد با یکدیگر تفاوت هایی دارند. این دو گرید براساس استاندارد شمش فولادی روسی GOST380 تولید شده و دارای مشخصات منحصر به فردی می باشند. در ادامه به بررسی آنالیز شمش 3SP و 5SP خواهیم پرداخت.
آنالیز شمش 3SP
شمش های 3sp انعطاف پذیری بیشتری نسبت به گرید دیگر داشته و به جهت خواص مطلوب از قیمت بالاتری نیز برخوردار می باشد. شمش 3sp یا st44-2 بار کربن حداکثر 22، اصولا بیشتر در تولید نبشی و ناودانی و یا در بعضی موردها در سایز های میلگرد های ریز استفاده می شود. همچنین در شمش های این گرید میزان عناصر آلیاژی کمتری نسبت به شمش 5SP به کار رفته است.
آنالیز شمش 5SP
اصولا شمش 5sp بیشتر برای تولید میلگرد تا سایز 25 مورد استفاده می شود و دارای انعطاف پذیری کمتری می باشد. برای تولید میلگرد سایز 25 به بالا از شمش با گرید Gr60 استفاده می شود. برای تولید کلاف نیز از شمش با گرید 5sp، Rst34، 1006، 1008 استفاده می گردد.
روش های تولید شمش فولاد
شمش های فولادی با دو روش استفاده از کوره القایی و قوس الکتریکی تولید و به بازار ارائه می شوند. هریک از روش های تولیدی دارای مزایا و معایبی بوده و شمش های تولیدی با هریک از روش ها خصوصیات خاصی خواهند داشت. در ادامه به بررسی روش های تولید شمش فولاد از آهن قراضه خواهیم پرداخت.
در ابتدا بهتر است بدانیم که سنگ آهن ماده اولیه تولید فولاد است. برای تولید فولاد باید فرآیند طولانی و سختی را از سر گذراند. بیشتر سنگ آهنی که در جهان استخراج می شود در کوره های بلندی مورد استفاده قرار می گیرند. در این کوره ها و طی فرآیندی، پس از مرحله پیش پخت و کلوخه سازی، کک و آهک را به کوره اضافه میکنند تا آهن و چدن را از سنگ آهن جدا کنند. بعد از آن، آهن خام به فولاد مذاب تبدیل می شود.
سپس ناخالصی های فولاد خام مانند کربن به وسیله اکسیژن را از آن جدا میکنند تا فولاد خام به دست آید. فولاد مذاب پس از جداسازی ناخالصی به واحد ریخته گری برده می شود تا مواد مذاب را در واحد ریخته گری داخل قالب ها ریخته و بر روی غلطکی قرار داده و با پاشیدن آب به خنک کردن آن اقدام می کنند. پس از خنک شدن شمش فولادی را به طول دلخواه برش می دهند. روش کوره الکتریکی و کوره القایی هم از دیگر روش های تبدیل سنگ آهن به فولاد است. بیشتر فولاد جهان به روش کوره بلند تهیه می شود اما در ایران از روش کوره الکتریکی استفاده می شود.
در نهایت تختال های تولید شده به طول های مورد نظر برش داده می شوند. آهن اسفنجی، که در تولید شمش فولادی مورد استفاده قرار می گیرد از طریق احیای مستقیم گندله تولید می شود. شمش سطحی ذوزنقه ای شکل است که طول هر شاخه آن حداکثر 2 متر است و تفاوت در شکل مقطع و ابعاد آن، نوع هایی را به وجود می آورد. ظرفیت کوره های قوس الکتریکی از یک کیلوگرم تا بیست تن متغیر است. به طور مثال فولاد کویر کاشان از روش قوس الکتریکی استفاده میکند که تفاوت قیمتی و کیفیتی زیادی با محصولات شمش کوره القایی دارد.
تولید شمش با استفاده از کوره قوس الکتریکی:
شمش حاصل از این روش از کیفیت بالاتری نسبت به کوره الکتریکی برخوردار است زیرا در آن یک مرحله آنالیز بیشتر انجام می شود. برخی از تولیدکنندگان بزرگتری مثل فولاد کویر کاشان که میلگرد آنها هم در بازار همان طوری که شاهد هستید از فاصله قیمتی بیشتری با بقیه تولیدی ها برخوردار می باشد از شمش کوره قوس الکتریکی برای تولید میلگرد استفاده می نمایند. در ادامه به بررسی تفاوت شمش قوس و القایی خواهیم پرداخت.
ظرفیت کورهای قوس از یک کیلوگرم تا بیست تن متغیر است. این کوره ها برای فولاد ریخته گری (ذوب کردن) کاربرد فراوان دارد. اما در خصوص شمش تولیدی به این روش با توجه ظرفیت اعلام شده و عدم امکان تصفیه مذاب، در این روش شمش های تولیدی از نظر آنالیز دارای پراکندگی زیاد در رنج استاندارد در یک محموله می باشند.
همچنین برخلاف کوره های القایی، کوره های قوس امکان تصفیه مذاب دارند که منجر به نتایج زیر می شود:
- امکان تولید شمش کم کربن
- رنج عناصر مضر مانند فسفر و گوگرد در شمش را به حداقل می رساند
- پراکندگی رنج آنالیز استاندارد را در یک محموله به حداقل می رساند
تولید شمش با استفاده از کوره القایی:
این کوره ها به دلیل غلیانی که که در آن ها وجود دارد، مشکل همگنی مذاب را ندارند. یکی از مشکلات تولید شمش با این روش این است که به دلیل غلیان، میزان اکسیژن محلول در مذاب بیشتر بوده که این موضوع سبب اکسید شدن می شود. با این حال در صورت کنترل میزان اکسیژن، مشکلی برای تولید با این روش وجود ندارد ولی معمولا اکسیژن در کوره های القایی کنترل نمی گردد. این اکسیژن در محصول نهایی ایجاد عیوب می کند.
یکی دیگر از مشکلات تولید شمش با این روش فسفر زدایی و گوگرد زدایی است. این دو عمل در دو شرایط مختلف (یکی با دمای بالای مذاب و دیگری در دمای پایین مذاب) انجام می شوند در نتیجه در صورتی که هم فسفر و هم گوگرد بالا باشد پایین آوردن میزان آن ها سخت می شود.
یکی دیگر از مشکلات تولید فولاد با کوره القایی، ماشین های ریخته گری مداوم هستند که تقریبا همگی ساخت چین یا هند یا ساخت داخل هستند و تکنولوژی آن ها قدیمی می باشد. به این دلایل گفته می شود که کیفیت شمش در کوره القایی پایین می باشد.
تفاوت شمش قوس و القایی
کوره القایی به خوبی نمی تواند اکسیژن را کننترل کند و همین امر باعث عیوبی در محصول می شود. به دلیل غلیان اکسیژن محلول در مذاب اکسید شدن فروآلیاژ پیش می آید. از دیگر مشکلات کوره القایی فسفر زدایی و گوگرد زدایی است. این دو عمل در دو شرایط مختلف (دمای بالا و پایین مذاب) انجام می شوند، که در صورتی که هم فسفر و هم گوگرد بالا باشد، پایین آوردن میزان آن ها کاری دشوار است.
برای برطرف کردن این مشکل می توان از کوره تصفیه پاتیلی استفاده کرد که کیفیت بالایی دارد ولی به دلیل اینکه این کوره ها برق، نسوز، الکترود و مواد افزودنی مصرف می کنند در فولادسازی ایران مورد استفاده قرار نمی گیرد. به این علت که هزینه زیادی در پی دارد. بیشتر ماشین های ریخته گری در کشور ساخت چین، هند و یا داخل هستند که تکنولوژی آنها قدیمی و بیش از سی سال دارد. تکنولوژی پایین، اتوماسیون ضعیف، طراحی ساده و… ایراداتی را به ریخته گری اضافه می کند که با عیوب ناشی از آنالیزسازی در کوره القایی ترکیب می شود و برای همین امر است که کیفیت شمش در کوره القایی پایین است.
چند نوع شمش در صنعت وجود دارد؟
سه نوع شمش فابریک، بلوم و سی سی ام وجود دارد.
در تولید میلگرد چه نوع شمشی مورد استفاده قرار می گیرد؟
در ساخت میلگرد 14 تا 40 شمش با 30 تا 35 درصد کربن و برای ساخت مقاطع با سایزهای پایین تر از شمش های با کربن کمتر استفاده می شود
تفاوت بین شمش کوره القایی و قوس الکتریکی در چیست؟
شمش حاصل از کوره به روش قوس الکتریکی از کیفیت بهتری نسبت به کوره الکتریکی برخوردار است زیرا در آن یک مرحله آنالیز بیشتر انجام می شود.
رواج پیدا کرده است؛ اما تولید هر محصول نهایی با کیفیت نیازمند فرآوردههای میانی تولید فولاد است، از آنجا که شرکتهای مختلفی شمش فولادی تولید میکنند محصولات با استانداردهای مختلفی در بازار وجود دارد، برای ما بنویسید کدام شرکت فولادی تولید بلوم، بیلت و تولید اسلب بهتر و با استاندارد بهتری دارد.